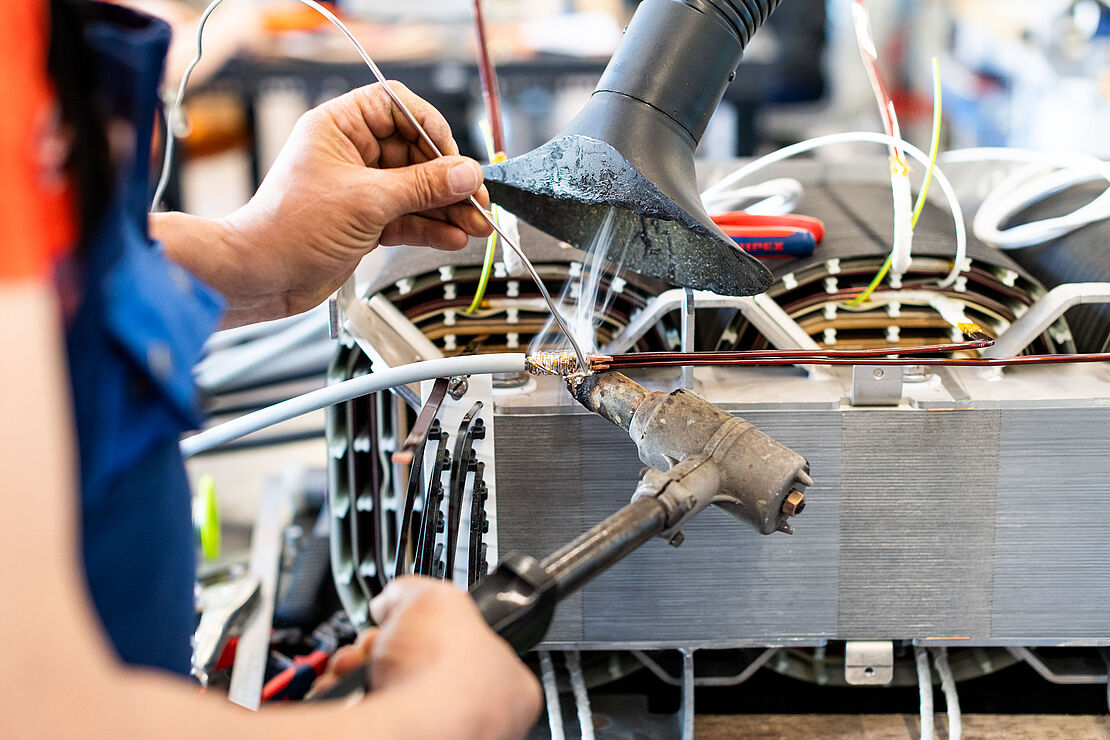
Repair
The repair of a transformer
A repair is the process by which a defective or damaged object, in our case a transformer, choke or filter, is restored to its original functionality and performance. Repairs can be carried out in different ways and to different extents, depending on the type of damage and the item affected. Here are some key aspects of the repair:
Share
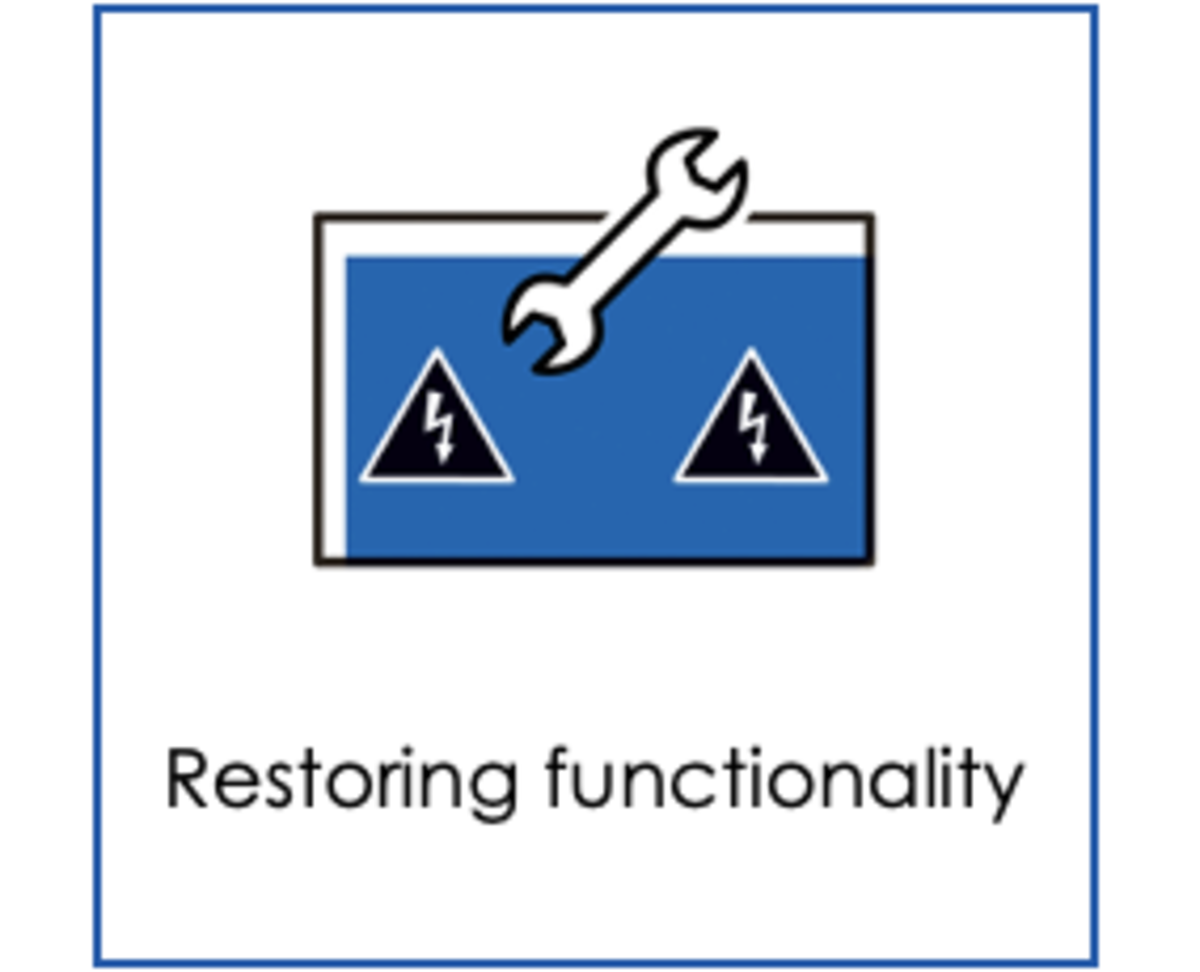
The main objective is to ensure functionality so that the product or system can be used properly and safely again. Bächli AG has the ability to analyse and examine products from other manufacturers, make repair suggestions and then repair the transformer or chokes professionally.
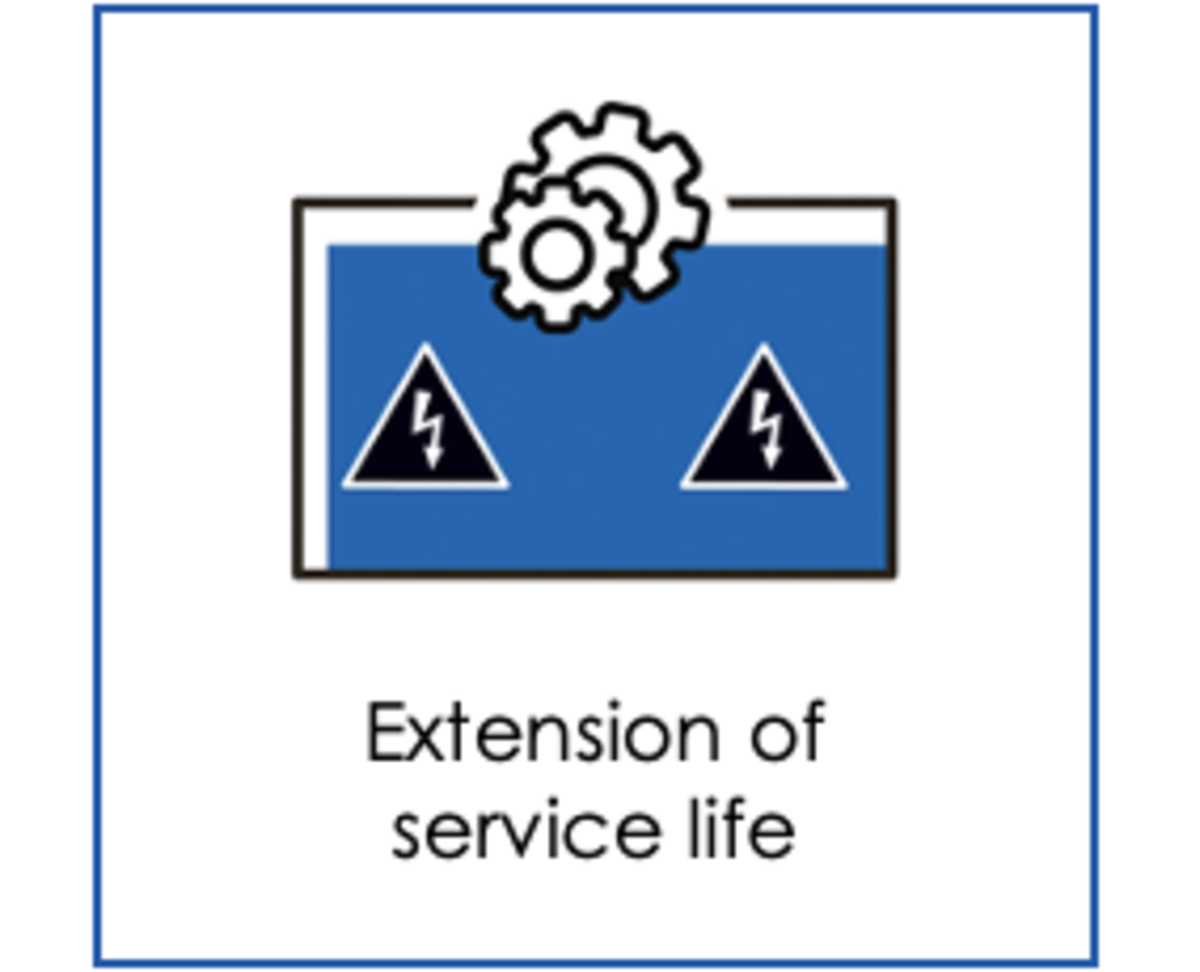
A repair extends the service life of the transformer. This is because the weak points are rectified, replaced or improved. Whether a product can be repaired must be weighed up carefully, as it is important that the standards and regulations and all safety conditions are complied with. It also only makes sense to repair a product if its service life is subsequently guaranteed for several years.
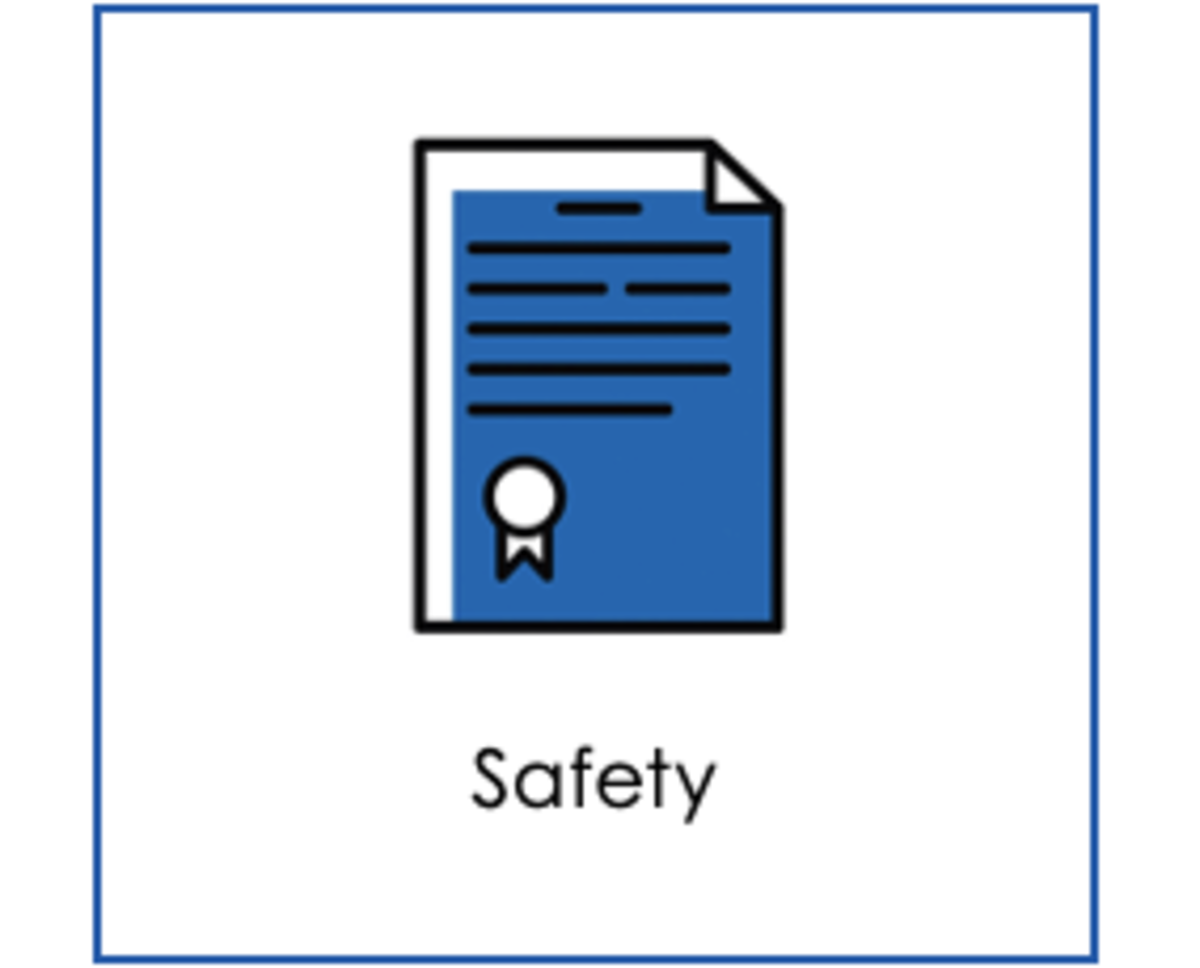
It is very important to ensure that the repaired transformer or choke is safe to use and can be operated without any safety restrictions in the system (machine, plant, vehicle). It is essential that all applicable standards and regulations are complied with.
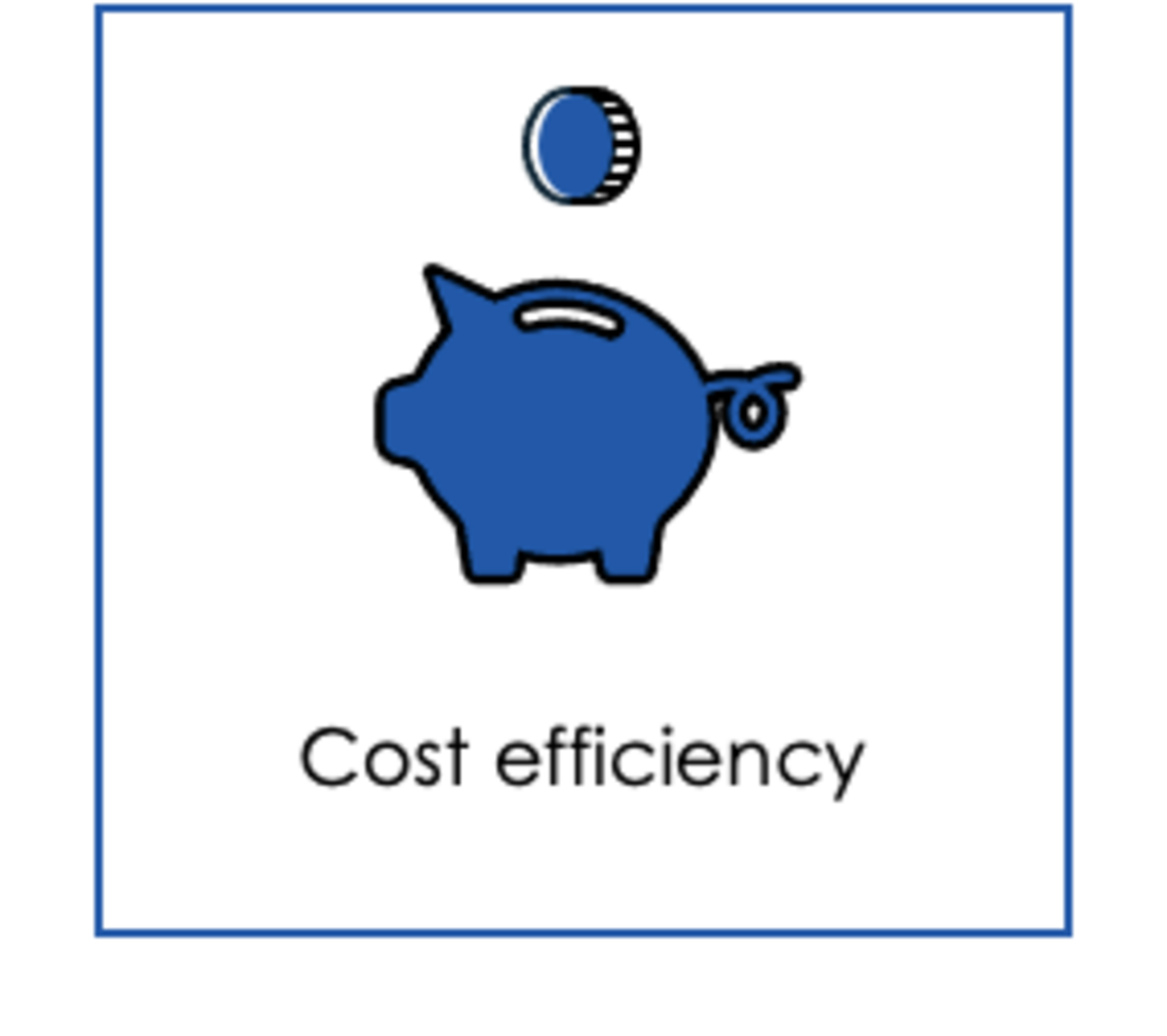
One positive effect is that the cost of buying a new object is avoided by repairing the existing one. This eliminates the purchase costs and results in lower repair costs, as well as extending the life cycle.
Why repair a transformer at all?
There are several reasons why it may make sense to repair a transformer instead of simply replacing it:
One of them is the cost savings. In many cases, repairing a transformer can be cheaper than buying a new product. For larger transformers in particular, the cost of replacement can be considerable.
At the same time, environmental awareness is also an issue. By repairing and reusing transformers, various resources can be saved and the environmental impact reduced.
Availability is a major challenge, especially at the moment. In some cases, it can be difficult to procure a specific type or size of transformer. Repair makes it possible to extend the useful life of the existing transformer until a suitable replacement can be found.
In situations where a transformer is essential to the operation of a plant or system, a repair can enable a quicker return to service than the purchase of a new device. This means that nothing stands in the way of a quick recommissioning.
In some cases, a transformer is a customised product that cannot simply be replaced by a standard model. Repair or reproduction is then the only practical way to get the appliance back into operation.
Ultimately, the decision to repair or replace a transformer depends on various factors such as cost, availability of spare parts, time frame and environmental considerations. These factors must be evaluated in order to make an appropriate decision.
Small repairs:
Minor repairs are understood to mean the repair of minor damage or malfunctions. This can often be carried out quickly and with minimal effort. Examples include replacing a fuse, replacing a terminal, etc.
Medium repairs:
This includes repairs that require more time and expertise and often require special tools or spare parts. Examples are the replacement of a bracket, replacement of a housing, etc.
Major repairs:
Major repairs are extensive and complex repairs that are preceded by a thorough examination and analyses. These may require the dismantling and replacement of several components. Examples include the complete repair of the transformer or the choke.

As a first step, our test laboratory and technical department will determine and identify the problem or origin and determine the cause, defect or damage. These investigations are carried out using various test equipment, analysed, evaluated and documented.
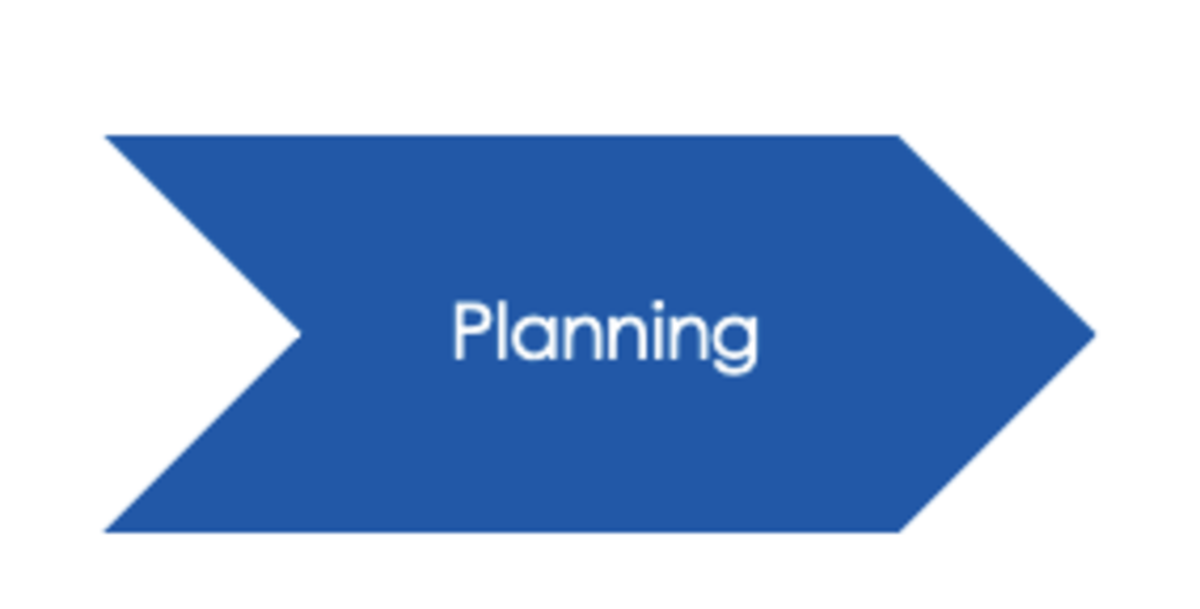
Following the fault analysis, planning is carried out to determine the necessary steps. The tools and materials required for the repair are recorded and clarified. From this, a production plan is drawn up, which plans the time phases and thus provides an overview of the duration and material requirements of the repair. The costs and other expenses can be derived from this.

The customer is offered two types of repair:
Basic offer
The defective transformer is repaired by Bächli or rebuilt 1:1. The previous scope of services is still covered. In addition to the product, the customer receives all the updated documentation for the repaired transformer.
Optimised offer
Thanks to a recalculation that makes the best possible use of the materials, Bächli optimises the defective transformer. This not only increases its performance, but also prevents future problems.
In addition to the quotations, the customer is also shown what the schedule looks like so that they can plan their processes and minimise downtime.
The customer also receives detailed documentation to accompany the optimised quotation.
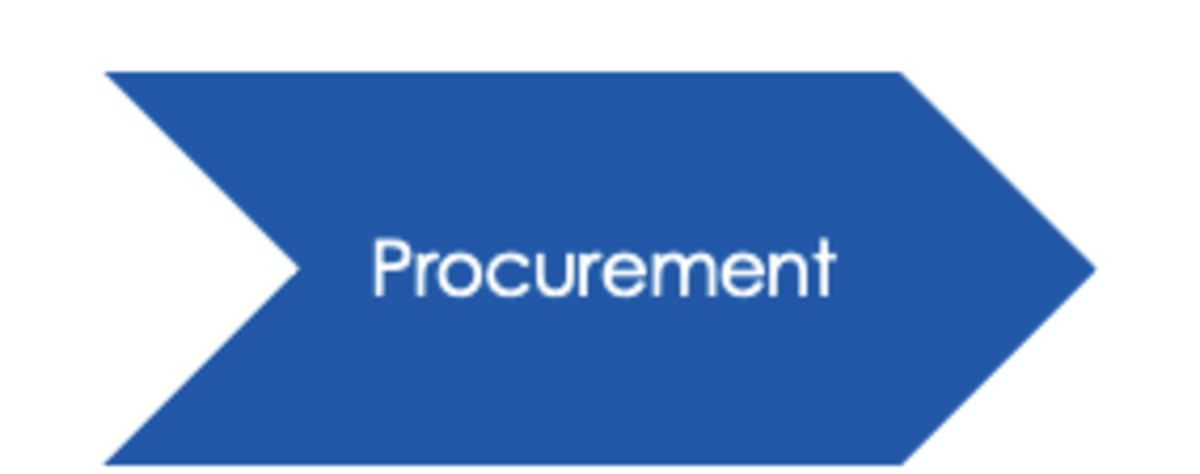
Bächli AG succeeds in optimising the time schedule through optimum process design so that the individual parts required for production are procured as quickly as possible. Through discussions with our suppliers, we try to optimise delivery times in order to guarantee the customer the shortest possible waiting time.

The repair work is carried out in accordance with the measures planned in development and AVOR in our production.
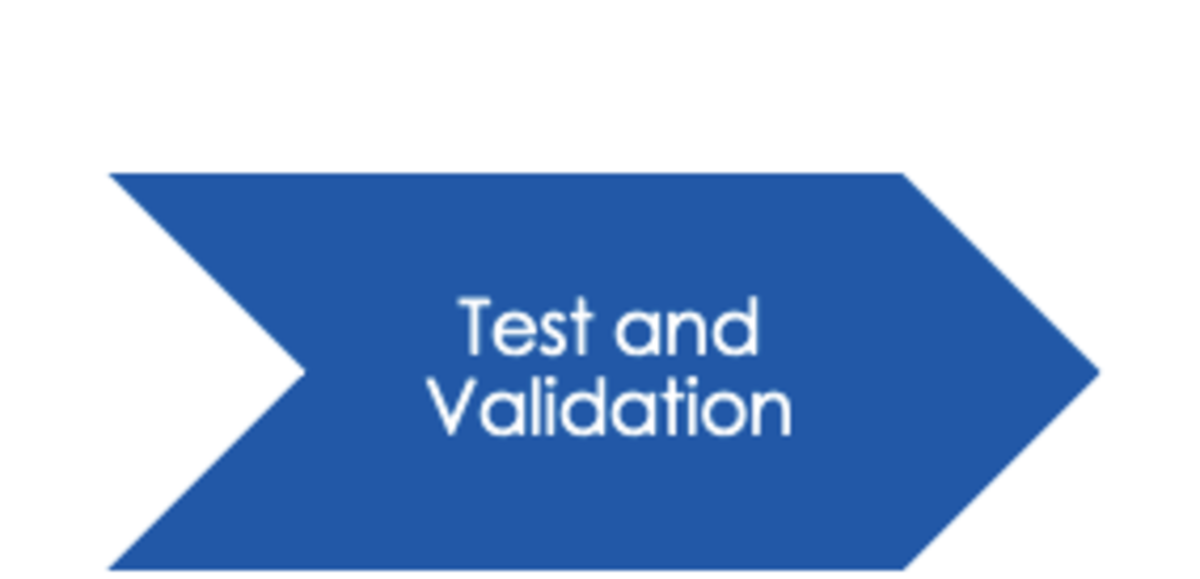
A comprehensive check of the functionality of each transformer or choke is arranged after the repair work has been carried out. This requires extensive testing to ensure that the object or system functions properly and is safe after the repair.
All necessary documents agreed with the customer are created and prepared for the customer.

By keeping thorough and comprehensive records of the work carried out and the results, we ensure that all steps taken and materials used are documented in a comprehensible manner. This means that a future reproduction is not a problem and can be easily realised.
We ensure that the documentation is stored for future reference.
Defective transformer - replacing individual parts
If only part of the transformer is defective and can be replaced, it often makes more economic sense to go down this route. Individual components such as fuses, windings, insulators or connections can be damaged and replaced relatively easily, which significantly reduces the overall cost compared to replacing the entire transformer.
In addition, replacing a single defective part can minimise the downtime of the transformer as no extensive repair work is required. As a result, the working time and waiting time for procurement is reduced many times over. This is particularly important in situations where continuous operation is crucial.
In many cases, the diagnosis and repair of a single faulty part can also help to extend the life of the transformer by preventing further damage.
Taking over as many parts as possible may well be a solution. We would therefore like to take a closer look at the three main elements of the transformer: winding, iron core and insulation.
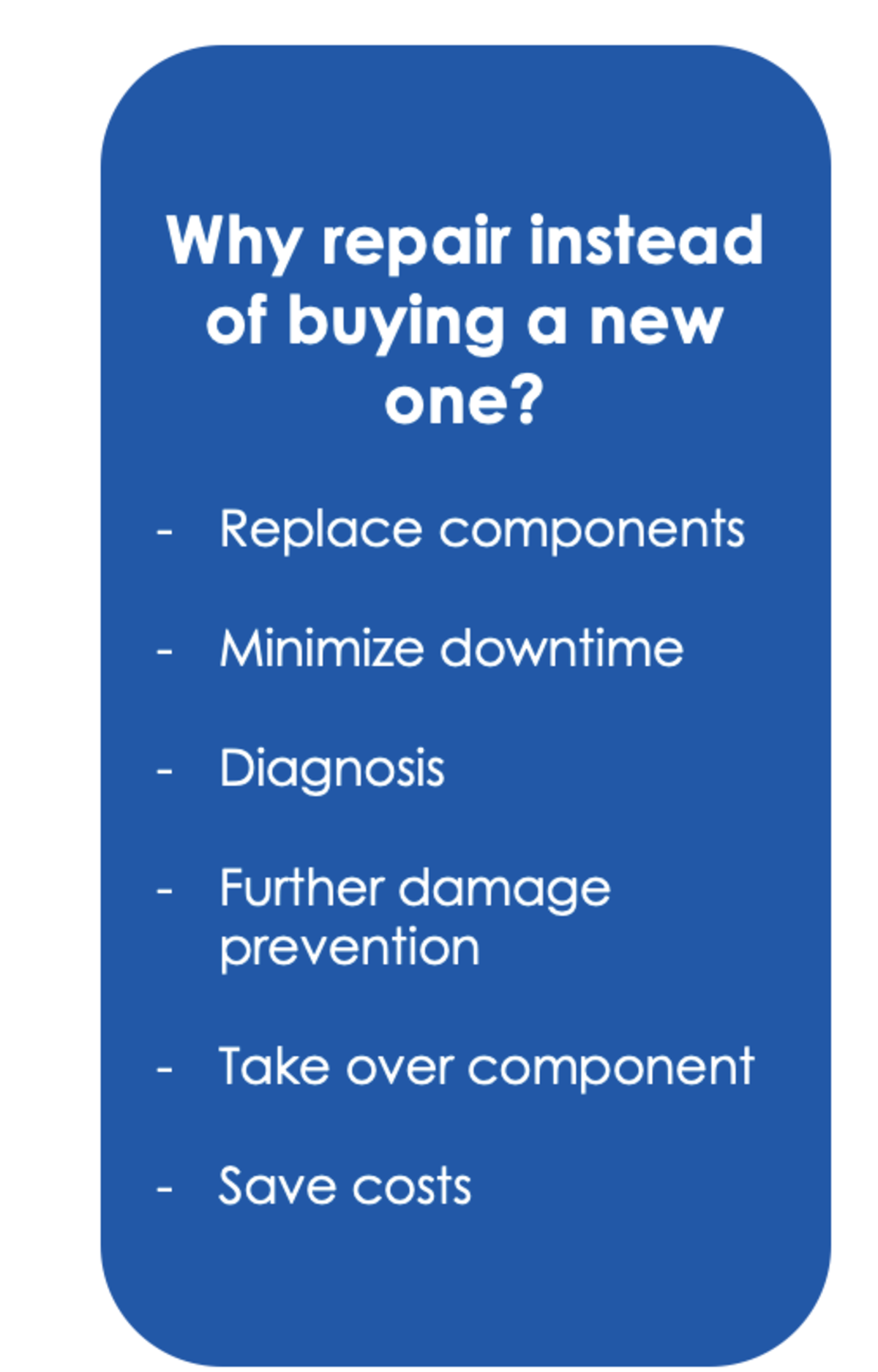
Cost efficiency
Manufacturing new coils is often expensive, as a lot of copper has to be replaced. It is therefore important to analyse well whether the other parts of the transformer are still intact, so it can make economic sense to continue using them.
Quick repair
If only the coils need to be rewound, this can often be done more quickly than a comprehensive repair of the entire transformer. This can minimise the downtime of the device, which is particularly important if the transformer is essential to the operation of a plant or system.
Maintaining quality standards
Rewinding the coils allows the quality and performance of the transformer to be maintained or even improved. This can significantly increase the reliability of the transformer.
Environmental friendliness
By reusing intact parts and rewinding coils instead of replacing the entire transformer, less waste is also generated, which is more environmentally friendly.
However, it is important to ensure that the rewinding of coils and reuse of other parts is carried out by qualified professionals to ensure that the repaired transformer functions properly and meets the required standards.
Replacing the iron core as part of a repair can be a sensible way to improve the efficiency and performance of a transformer. Here are some reasons why this might be considered:
Improved performance
A new iron core can have a higher magnetic permeability or be made of a higher quality material, which improves the magnetic properties of the transformer. This can lead to a more efficient transfer of energy and increase the efficiency of the transformer.
Reduced loss
A higher quality iron core can help to reduce iron losses in the transformer, particularly hysteresis losses and eddy current losses. This effect could lead to lower overall heat generation and extend the service life of the transformer.
Adaptation to new requirements
In some cases, a transformer may need to be adapted to new requirements, e.g. to cope with higher power levels or to enable operation in environments with special requirements. A new iron core can help make these adjustments to achieve the desired performance parameters.
Better compatibility
By replacing the iron core, the transformer can become more compatible with modern control and monitoring systems. This makes it easier to integrate the transformer into existing or new systems and improves the overall functionality of the component.
Environmental friendliness
A new iron core can be made from materials that are more environmentally friendly or have better recyclability. This can contribute to the environmental impact of the transformer and thus reduce the consumption of resources over its entire service life.
However, it is important to note that replacing the iron core is often a complex and costly operation that may not be economically viable in all cases. Careful cost-benefit analyses should therefore be carried out before carrying out such a retrofit project
Improved safety
Improved insulation can reduce the risk of short circuits or other electrical malfunctions that could lead to accidents. Increased safety is particularly relevant in environments where people are working or are in the vicinity of the transformer.
Protection
Additional insulation ensures that the transformer is better protected against environmental influences such as moisture, dust and other contaminants. This extends the service life of the transformer and increases its reliability, especially in harsh or demanding environments.
Reduction of noise generation
Good insulation can also help to reduce the operating noise generated by a transformer. This is particularly important in environments where noise levels need to be minimised, such as residential or office environments.
Improving heat dissipation
Another plus point is an improvement in heat dissipation. Improved insulation can also help to optimise the heat dissipation of the transformer, which can lead to a lower operating temperature and improved performance overall.
Norms and standards
Norms and standards also change over time. This can lead to a situation where the insulation no longer meets current standards during a repair and needs to be improved. By adding insulation, the transformer may be able to meet or exceed these standards.
However, it is important to note that insulating the entire transformer as a measure can be technically challenging and costly depending on the size and complexity of the transformer as well as the specific requirements of the project. A thorough assessment of the costs and benefits should be carried out before embarking on such a project.
To summarise, repair is an important process for restoring functionality and extending the service life of objects and systems. It offers numerous benefits, particularly in terms of sustainability and cost efficiency, but can also present challenges.
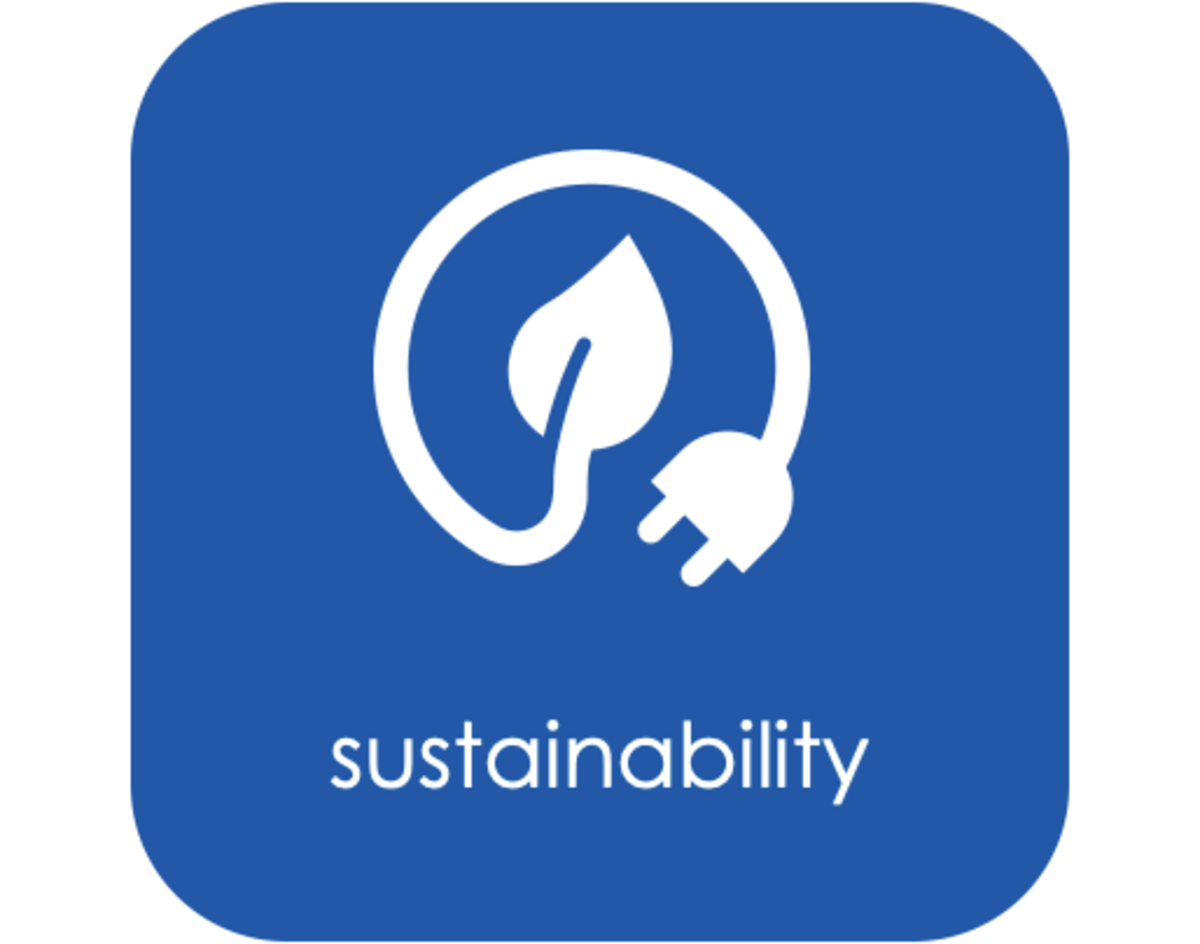
The transformer or the choke are components that have a very high recyclable material content. This effect reduces waste and the need for new resources, as existing items can be reused and new components have a long service life.
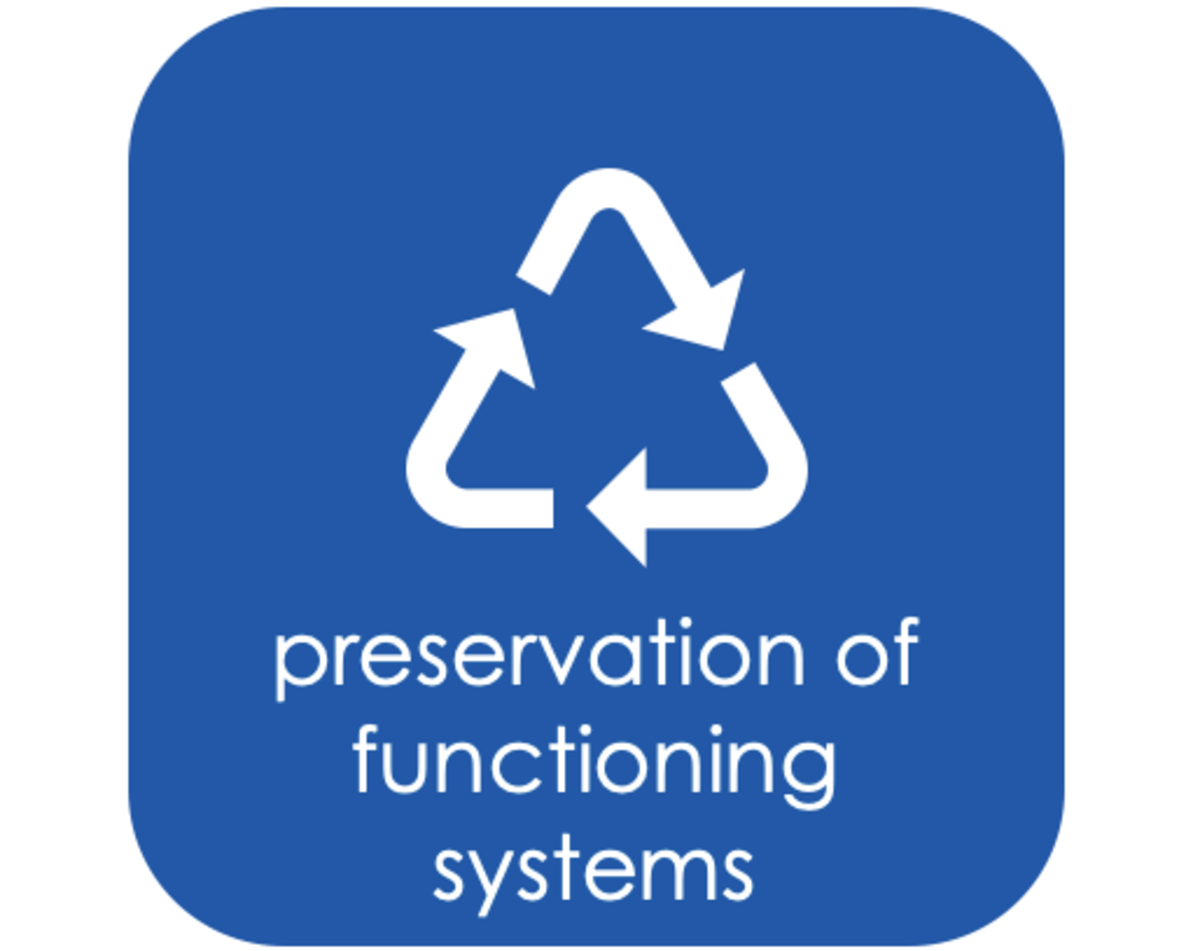
Transformers and chokes are often installed in systems that have a long service life and must function reliably. It therefore often makes sense to repair a functioning system for as long as possible, as you can then rely on its functionality and reliability. However, with new systems you always have to deal with start-up problems and unreliability.

Some repairs require specialised knowledge and expertise. As Bächli AG can look back on over 70 years of company history and therefore has a lot of experience in the field of winding goods, the expertise and knowledge in development and also in production is well-founded and extensive.